For an amateur or less of a naïve person, a good pair of sawhorses is an intrinsic component of any project. Steve Ramsey of Woodworking for Mere Mortals takes the simple and hassle free task of making one’s own sawhorses one step further.
See Also:
The only genuine problem or difficulty with basic sawhorses is that they take up a lot of room in your garage or shop, wherever you store them. This simple folding sawhorse design from Steve is very easy, quick, prompt and will solve the storage problem that the basic sawhorses cause.
Over here, you will get to know how to build a folding sawhorse quick and easy.
More...
All you require for building a folding sawhorse
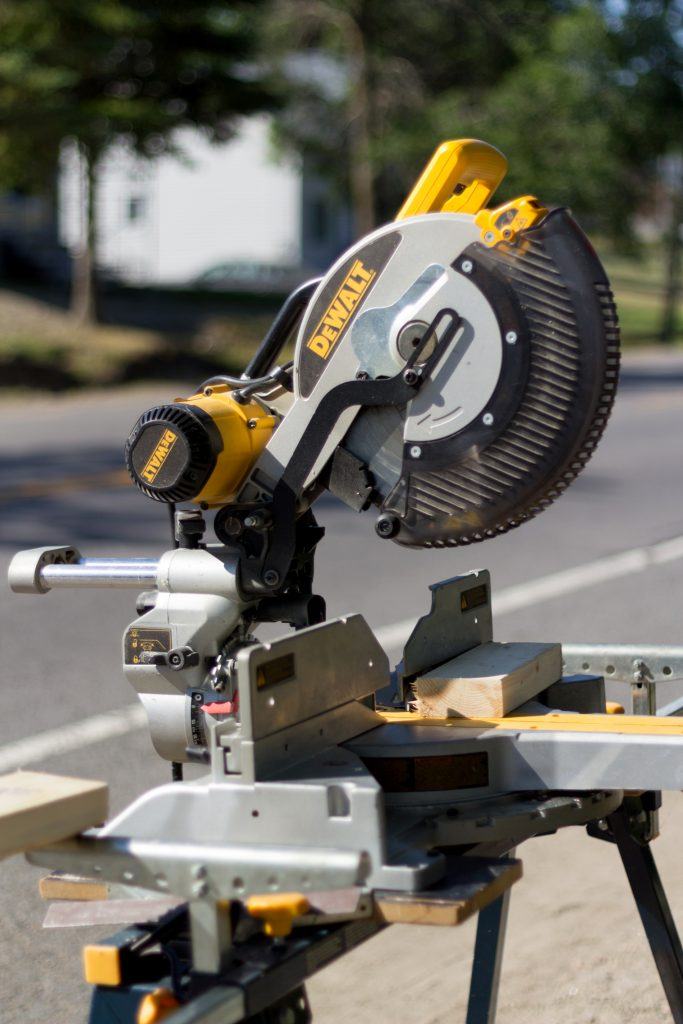
DeWalt miter saw
- 2- 2x4x8’s
- One ½ inch 4x4 sheet of plywood
- Two ½ inch screws
- Two 3 inches strap hinges along with screws.
- Four 2 inches x ½ inch dowels
- Cordless drill
- Miter saw or table saw
- Band saw or jigsaw
- Wood glue
#1. Cut the 2x4x8’s
As mentioned earlier, you only need two 2x4x8's for each sawhorse. The best and ideal way to start is to cut all of your base material in the very beginning.
- Sawhorse Base:
2x4x8 number one- cut into 3 equal lengths at 31.5 inches.
2x4x8 number two- cut one piece at 31.5 inches, and another piece at 48 inches. - The Shelf: The remaining section of 2x4x8 number two will need to be cut into four strips at 3/4 inches wide 15 inches long.
Or, if you do not wish to go through a great deal of trouble involved in cutting of a 2x4 into strips, just purchase a 1x2 strip and cut it to the required length.
The shelf should be a 1/2 inch plywood rectangle at 13.5 inches x 27.5 inches.
#2. Cutting 19-degree angles
Using a ta or miter saw, cut the ends of each 31.5-inch board at an accurate 19-degree angle. The angles should be parallel to each other on each board. ble saw
Make sure you are not changing or making any form of alterations in the overall length of each board.
#4. Pre-drilling and securing 3 inches strap hinges
Using a straight edge, draw a straight line 4 inches from each edge of the 48 inch by utilizing the brace board in order to mark where the sawhorse legs will be attached.
Centering your leg on the top board and, using the rightful strap hinge, pre-drill the holes where the hinge will be attached to the leg and the brace board as well.
#3. Drill pocket holes
Drill pocket holes on one end of each 31.5-inch leg to connect the leg to the top of the sawhorse.
Simply make sure that you are using the correct bit or portion for the size
screw you will use.On that same note, be sure to use a screw adequately long to penetrate both boards, however not long enough to drill all the way through the entirety of the top board.
#5. Marking line halfway down each leg
Now you should have your legs ready to modify for the shelf. By using a straight line edge, mark a line halfway down the sawhorse legs.
This is where you will start drilling the holes for the dowels that will hold up the shelf brackets steadily and firmly.
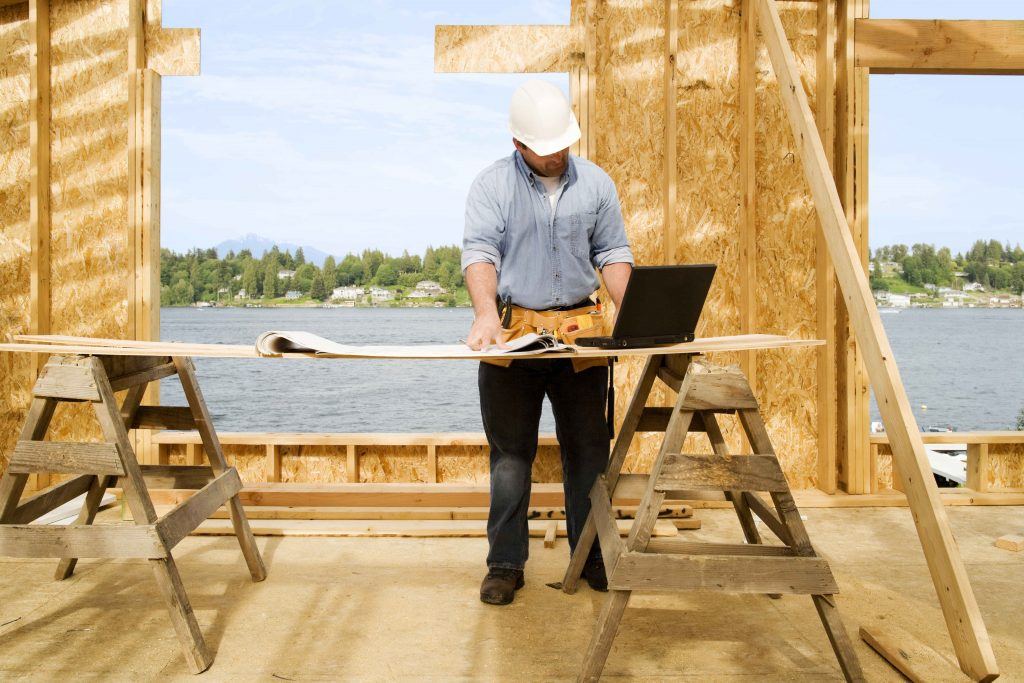
#6. Drilling holes for dowel rods
Drill a 1/2 inch hole in the center of each line on your legs. Make sure you remember that if you are using a different sized dowel rod, you ought to adjust the size of the hole.
For instance, if I am using 3/4 inch dowels, I need to invariably drill a 3/4 inch hole.
#7. Attaching dowel rods
Prior to hammering in the dowel rods, make sure you add the optimum amount of wood glue in the holes.
Now, place the dowel rods in each hole and lightly tap the surface unless all dowels are seen to have gained the approximately same length.
If there is excess glue, wipe it off.
#8. Secure legs onto top sawhorse brace
You have already done with these steps, in case you do not remember, go through the aforementioned information.
Once done, repeat the steps and attach the legs to the top of the brace.
At this point, the sawhorse is extremely sturdy. However, there will be a maximization of sturdiness and power once the shelf is added.
#9. Drilling holes, notch and attaching shelf brackets
Using the sawhorse legs as per the guidance, hold your 15-inch strips against the center line on the prevailing legs and mark where you will begin drilling each hole to attach on to the dowel rods.
Drill holes for the dowel rods and on one of the holes on each board, notch out a clear cut hole in order to lift off the dowel rod easily.
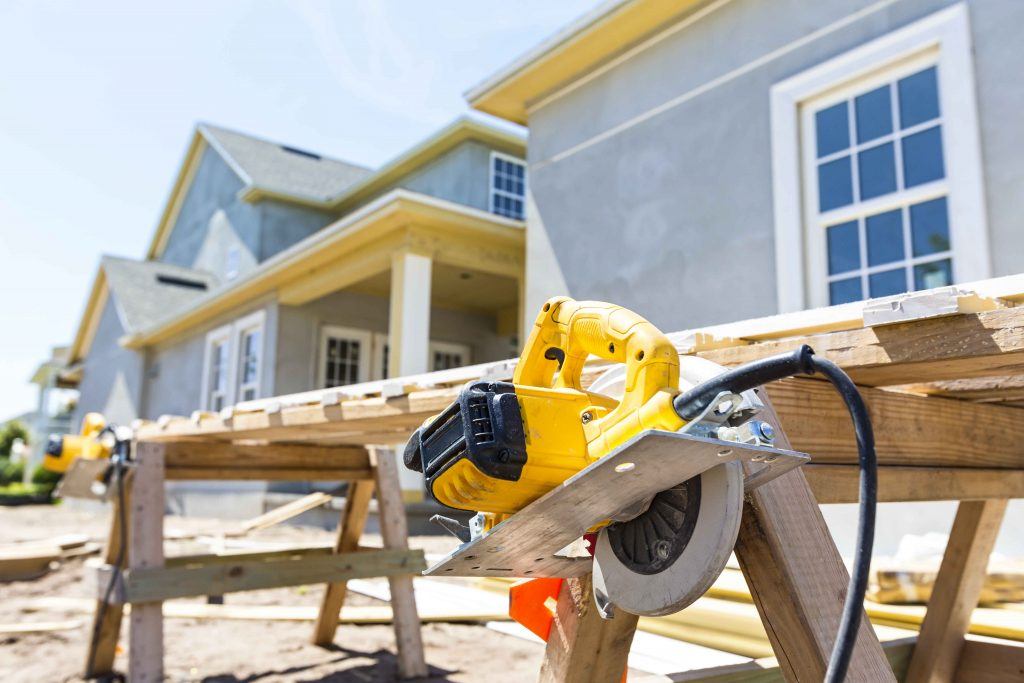
#10. Securing plywood shelf
Now, go on to secure your 13.5-inch x 27.5-inch plywood shelf onto the brackets. Make sure that you do not screw into the dowel rods or perhaps your shelf will not be able to fold as it should have been.
You are done with creating the folding sawhorse, relax on your couch and see the wonders of the tool.
Features, characteristics, and nature of
some of the well-known sawhorses
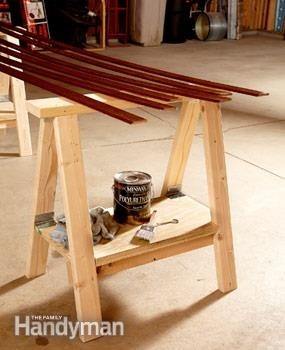
Saw Horse Model via Family Handyman
Some sawhorses have a shelf and some fold up, but Jeb's design (the illustration given above) combines both features.
And he is right when he says these horses are fun to build.
To make a pair, you will essentially need a 4 x 4-ft. a sheet of 3/4-in. plywood, one 8-ft. 2x6, one 8-ft. 2x4, two 12-ft. 2x4s and eight hinges.
- Features: Easily foldable, includes a shelf, fun to build.
- Cost: Around $40 per sawhorse.
- Time required: In and around an hour.
- Skill level: From beginner to intermediate.
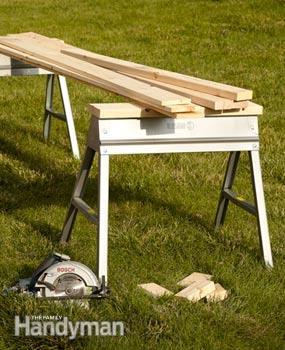
Space-saving Saw horse via Family Handyman
These metal foldable sawhorses which are a wonder of Travis’ imaginations can be hung on a wall or stacked perfectly in a corner.
In case you have to drag horses from one job to another, these are the ones for you.
However, be careful not to pinch a finger while folding them up. Travis is particularly fond of the EBCO brand—he claims to own a bundle of them.
- Features: Economical and reasonably priced, conveniently foldable, powerful.
- Cost: $18 approximately plus the cost of the top board too.
Framing carpenters usually build thwhich are an outcome of Mark’s creating abilities and skills. These are used when they show up at a job site. They leave them behind for the other subcontractors to utilize and then build new ones at their next job. ese horses
It is not quite unusual for the new homeowner to inherit a pair and hold on to them for several years.
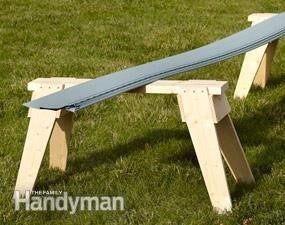
Saw Horse via Family Handyman
- Features- Inexpensive, super strong and easy to be built
- Cost- $12 each
- Time required- !0 to 15 minutes by using a pneumatic nail gun
- Skill level: Beginners
Here is a design that's been around for a thousand of years, perhaps longer. It is low, so you can use your knee to hold down your work. This sawhorse was primarily the consequence of Ken’s productive skills and designs.
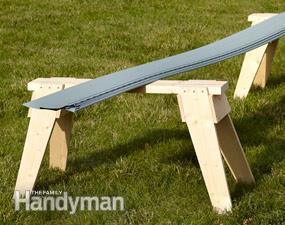
Saw Horse Sample via Family Handyman
The compound miters make this one a little trickier to create than the others.
However, if you take one part or element at a time and label them as you go, in a couple of hours you will have a pair or probably bundles of sawhorses that your own children will be proud to replicate someday.
We have simplified this one a little bit in order to avoid complications and complexities. On the version Ken made, the legs are mortised into the edge of a non-tapered top board. To make this horse, you need one 8-ft. 2x6 and two 8-ft. 1x6s.
- Features: Inexpensive, elegant and relatively lighter, easily stackable, pretty strong
- Cost- $12 per sawhorse
- Time required: one hour
- Skill level- Intermediate
Earlier in this articles, the materials required for the project of creating a folding sawhorse has been rightfully mentioned, enumerated below are the required tools in order to carry out the project successfully and with perfection.
- Hammer
- Miter saw
- Air compressor
- Air hose
- Cordless drill
- Circular saw
- Framing square
- Hearing protection
- S?afety glasses
Bottom line: Verdict
Sawhorses have a ton of uses and benefits and can be used to build or create an outdoor work station, small scaffolding, table saw out feed tables and as cutting surfaces which people do not mind marring.
The aforementioned sawhorse plans require little more than a circular saw and some 2 x 4s and plywood to build. Most of these sawhorses are also feasibly stackable so they can be conveniently stored when not in use without the discomfort and anxiety of the user/ owner.
The sawhorses are so very sturdy and durable that they can survive huge concrete logs or angular marks.